化工实验室中的配方和工艺在进入量产阶段时,往往面临诸多挑战,如数据传递不准确、工艺参数难以复现、生产效率低下等。为了解决这些问题,化工企业引入了化工PLM系统,通过其强大的数据管理能力和流程优化功能,实现实验室配方到量产的无缝衔接。那么,化工PLM怎样实现实验室配方到量产呢?
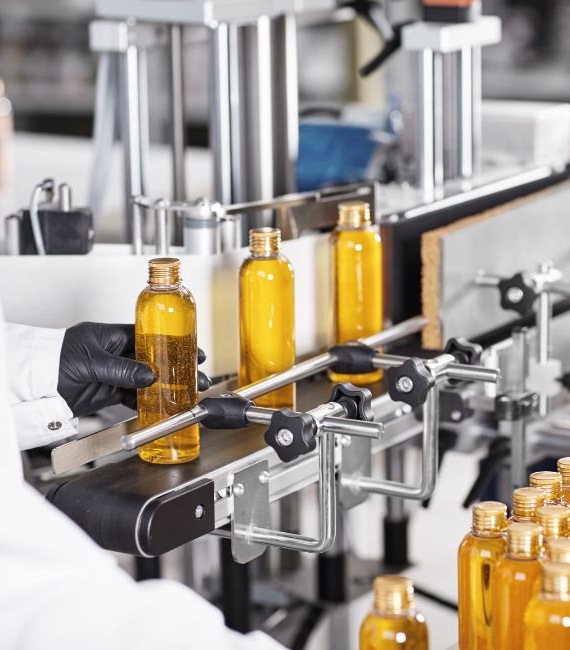
一、数据标准化与完整记录
实验室中的配方和工艺数据往往分散在各个实验记录本或电子文档中,难以形成统一的管理体系。PLM系统通过数据标准化,将实验室中的各类数据整合到一个统一的平台中,确保数据的完整性和一致性。无论是原材料信息、配方比例,还是工艺参数,所有数据都可以在PLM系统中进行记录和追踪。这不仅为后续的量产提供了可靠的数据基础,还能避免因数据传递错误导致的生产问题。
二、工艺的可重复性与优化
实验室中的工艺往往是以小批量或样品形式进行的,而量产则需要确保工艺的稳定性和可重复性。PLM系统通过模拟和验证功能,帮助企业在实验室阶段对工艺进行优化,确保其在量产阶段能够顺利实施。此外,PLM系统还能够对生产过程中的各项参数进行实时监控,及时发现并调整偏差,确保生产过程的稳定性。通过这种方式,PLM系统不仅提高了工艺的可重复性,还减少了生产中的废品率和返工率。
三、配方与工艺的无缝传递
从实验室到量产,配方和工艺的传递是关键一步。PLM系统通过内置的工作流引擎,将实验室中的配方数据和工艺参数无缝传递到生产环节。研发人员只需在PLM系统中完成配方的录入和工艺的确认,生产人员即可直接获取相关信息,避免了传统方式中可能出现的信息遗漏或误解。此外,PLM系统还能够对配方和工艺的每一次调整进行记录,确保数据的透明性和可追溯性。
四、协同与跨部门协作
实验室与量产之间的衔接不仅仅是数据的传递,还需要多个部门的协同配合。PLM系统为研发、生产、质量控制等部门提供了一个统一的协作平台,确保各部门之间的信息共享和高效沟通。例如,研发人员可以在PLM系统中共享实验数据,生产人员则可以根据这些数据制定生产计划,而质量控制部门则能够实时监控生产过程中的各项指标。这种协同工作方式不仅提高了工作效率,还减少了因信息不对称导致的误解和延误。
五、质量控制与合规性管理
化工行业的生产过程受到严格的法规和质量标准的约束。PLM系统能够帮助企业实时监控生产过程中的各项参数,确保产品符合相关法规要求。例如,某些化学物质的配比可能受到环保法规的限制,PLM系统可以实时提醒生产人员调整工艺,避免因违规操作导致的产品质量问题。此外,PLM系统还能够对生产过程中的每一个环节进行记录,确保生产过程的透明性和合规性。
六、自动化与智能化生产
随着工业4.0的推进,自动化和智能化生产已成为化工行业的发展方向。PLM系统通过与生产设备的无缝集成,能够实现生产过程的自动化控制。例如,PLM系统可以根据实验室中的配方数据,自动调整生产线上的设备参数,确保生产过程的稳定性和一致性。此外,PLM系统还能够通过数据分析,预测生产中的潜在问题,并提前采取措施进行调整,从而进一步提高生产效率。
化工PLM系统作为一种强大的管理工具,已经在实验室配方到量产的衔接中发挥了重要作用。通过数据的标准化记录、工艺的优化与可重复性验证等,PLM系统帮助化工企业实现了从实验室到量产的平稳过渡。在化工行业的复杂生产环境中,PLM系统不仅提升了生产效率和产品质量,还为企业提供了强大的数据支持和流程优化能力。